Ceramic saddle is improved from the arc saddle, it changes the both arched surface to rectangular surface and makes the interior and exterior radius of curvature different, this construction overcomes the problem of nesting basically, it makes porosity distributed even and improves the distribution of the fluid , greater capacity and lower pressure drop than Raschig ring.
They are available in variable sizes such as (mm): 12,16,19,25,38,50,76
Chemical Analysis
SiO2
|
>73%
|
Al2O3
|
17-25%
|
Fe2O3
|
<1.0%
|
CaO
|
<0.5%
|
MgO
|
<0.5%
|
K2O+Na2O
|
2-4%
|
Other
|
<0.1%
|
|
|
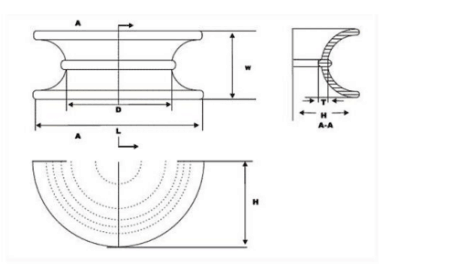
Physical Properties
Nominal size(inch)
|
1/2"
|
3/4"
|
1"
|
1-1/2"
|
2"
|
3"
|
Width(mm)
|
13±2
|
20±3
|
20±3
|
34±4
|
43±4
|
70±6
|
Height(mm)
|
13±2
|
20±3
|
20±3
|
34±4
|
43±4
|
70±6
|
Length(mm)
|
21±3
|
28±5
|
38±4
|
55±4
|
78±6
|
114±8
|
Thickness(mm)
|
2.0±1.5
|
3.0±1.5
|
3.0±2
|
4.0±2
|
5.0±2
|
9.0±2
|
Number per m3
|
610000
|
146000
|
59000
|
19680
|
8243
|
2400
|
Package density (kg/m3)
|
780
|
700
|
650
|
600
|
580
|
530
|
Free volume (%)
|
68
|
75
|
77
|
80
|
79
|
75
|
Surface area (m2/m3)
|
647
|
350
|
254
|
180
|
120
|
91
|
Specific gravity (g/cm3)
|
2.25~2.35
|
Water absorption (%)
|
<0.3
|
Acid resistance (%)
|
>99.6
|
Max operating temp.
|
1100℃
|
Porosity (%)
|
<1
|
Moh’s hardness (scale)
|
>6.5
|
Thermal conductivity(w/m.k)
|
0.9-1.0
|
Specific heat (j/kg℃)
|
850-900
|
Advantage
These saddles are made from chemical porcelain and have excellent resistance to acids except in the case of hydrofluoric acid.
Moisture absorption must less than half a percent.
The porcelain’s specific gravity is 2.3-2.4g/cm3 and an average heat capacity (between 20℃ and 500℃ of 0.22 cal/g.℃)
ceramic saddles for RTO’s softening point is 1400℃ min. And they show good thermal shock resistance during repeated cycling between 20℃ and 820 ℃.
Thermal shock test for saddles for RTO’S
For example shipping the saddles over 80 M3:
Randomly pick 100-200 pieces of ceramic saddles for RTO’s from the batch or shipment
For each sample selected, heat it up to 820℃ and maintain them at this temperature for 30 minutes
Drop the hot pieces into cold 20℃ water
Repeat steps 2 & 3 for10 times on each and every piece in the sample lot.
Examine the pieces and count the percent that show clear signs of breakage and/or cracking. Our standard is “less” than seven (7%) percent.